how a carbon fiber pickleball paddle is manufactured.
Pickleball, a rapidly growing sport combining elements of tennis, badminton, and table tennis, demands lightweight yet durable equipment. Carbon fiber paddles have become popular due to their exceptional strength-to-weight ratio and precision. Below is a step-by-step overview of how a carbon fiber pickleball paddle is manufactured.
1. Material Preparation
The process begins with selecting high-quality carbon fiber sheets (prepregs), which are pre-impregnated with epoxy resin. XXT is a professional carbon fiber manufacturer, we produce high quality carbon fiber, to ensure good pickleball paddles for customer. Additional materials like honeycomb cores (often polymer or Nomex®) and edge guards are prepared for structural support and impact resistance.
2. Design and Mold Creation
A paddle design is finalized using CAD software, specifying dimensions, weight distribution, and surface texture. A **mold** is then CNC-machined from aluminum or composite materials to match the paddle’s shape. The mold’s surface is polished to ensure a smooth finish on the final product.
3. Layering the Carbon Fiber
Carbon fiber sheets are cut into precise shapes using laser or hydraulic cutting tools. Workers layer the sheets into the mold, alternating orientations (0°, 45°, 90°) to maximize strength and stiffness. A **honeycomb core** is sandwiched between the carbon fiber layers to reduce weight while maintaining rigidity.
4. Curing in an Autoclave
The layered mold is placed in an **autoclave**, a high-pressure oven. Heat (typically 250–350°F) and pressure (up to 100 psi) activate the resin, bonding the layers into a single structure. This step eliminates air bubbles and ensures uniform density.
5. Trimming and Shaping
After curing, the paddle is removed from the mold. Excess material is trimmed using CNC machines or water jets to achieve the final shape. The edges are smoothed, and holes for grip assembly are drilled if required.
6. Surface Treatment
The paddle face undergoes surface texturing—either a **grit coating** (applied via spray or adhesive) or a molded pattern—to enhance ball spin. The surface is then sealed with a protective clear coat to prevent delamination.
7. Handle Assembly
A pre-molded **ergonomic handle** (often wrapped with cushioned tape) is attached to the paddle using epoxy adhesive. The handle’s weight and grip circumference are calibrated for player comfort and control.
8.Printing
Printing a logo or pattern is also a important step. We have Screen printing, hot stamping, laser craft, so we can print various customized logos.
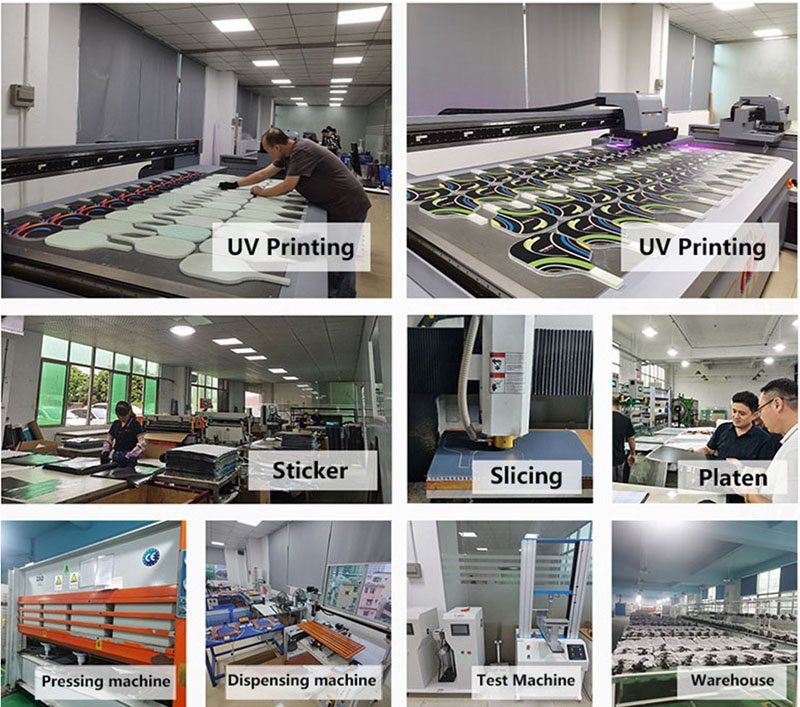
9. Quality Control
Each paddle undergoes rigorous testing:
Weight check: Ensures compliance with official standards (7.5–14 oz).
Balance test: Verifies the center of gravity aligns with design specs.
Durability test: Repeated impact simulations assess resistance to cracking
We are a original manufacturer of pickleball paddle, we provide brand pickleball paddles for many famous brands, if you want custom pickleball paddles, pleale contact us for free.